Exploring the World of Tooling Molding in Metal Fabrication
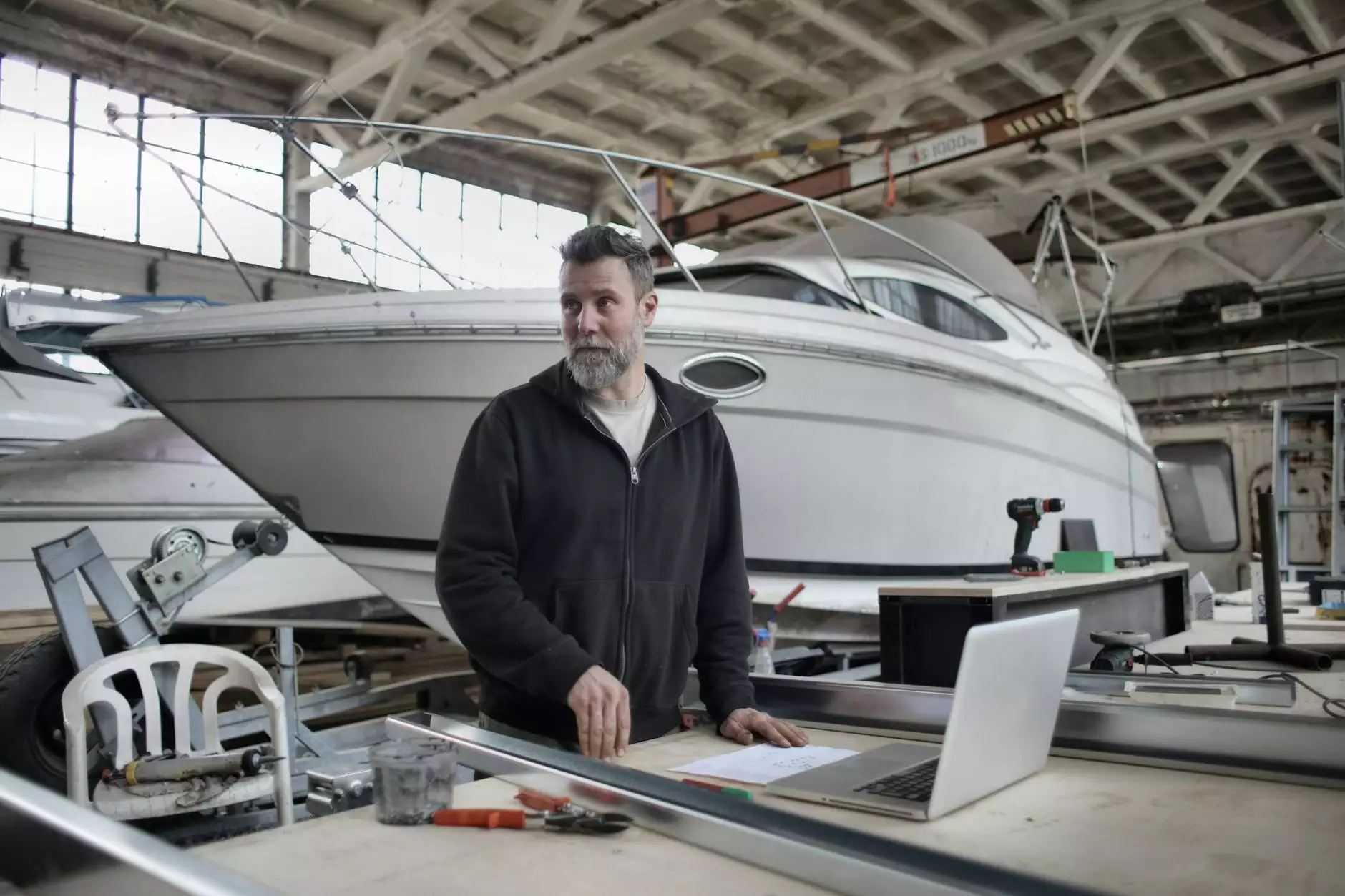
The field of metal fabrication is vast and intricate, with numerous techniques and technologies contributing to the efficient production of high-quality parts and products. One of the cornerstones of this domain is tooling molding, a sophisticated process that plays a pivotal role in the creation of molds used for shaping various materials, primarily metals. In this article, we delve deeply into the nuances of tooling molding, its importance in the metal fabrication industry, and how businesses like DeepMould.net are setting the standard in this specialized area.
What is Tooling Molding?
Tooling molding refers to the process of designing and manufacturing molds that are used to shape materials into specific forms. This technique is crucial in producing metal components, ensuring that they meet the precise dimensions and tolerances required by various industrial applications. The process includes several key steps:
- Design: CAD (Computer-Aided Design) software is used to create a detailed mold design that meets the specifications of the final product.
- Prototyping: A prototype mold is often created to test the design, allowing for adjustments before mass production.
- Manufacturing: The mold is then manufactured using high-quality materials, such as steel or aluminum, which can withstand the extreme conditions of metal shaping.
- Testing: After manufacturing, the mold undergoes rigorous testing to ensure it performs accurately under production conditions.
The Importance of Tooling Molding in Metal Fabrication
In the metal fabrication industry, tooling molding serves several essential purposes:
1. Precision and Accuracy
Tooling molding allows for the creation of molds that can achieve high precision and accuracy in part manufacturing. This level of detail is crucial in industries like aerospace and automotive, where any discrepancy can lead to significant issues.
2. Cost Efficiency
By using tooling molding, companies can significantly reduce waste and production costs. The ability to create durable molds that can be reused multiple times means that businesses can produce parts more economically over their lifecycle.
3. Enhanced Production Speed
The use of expertly crafted molds allows for quicker production times. Once the mold is created, successive parts can be produced in rapid succession, improving overall throughput and meeting client demands.
Types of Tooling Molding Techniques
There are several popular techniques within the category of tooling molding, each suited for different applications:
1. Injection Molding
Injection molding is a process where molten metal is injected into a mold cavity. This technique is chiefly used for creating complex parts with intricate details, making it a favorite in industries such as electronics and consumer goods.
2. Blow Molding
Blow molding involves inflating heated plastic or metal within a mold to create hollow parts. This technique is commonly applied in producing containers and packaging solutions.
3. Compression Molding
In compression molding, materials are placed into an open mold and then heated and pressed into shape. This method is particularly effective for producing large, solid parts.
Key Factors Influencing Tooling Molding Processes
The success of tooling molding depends on several critical factors:
1. Material Selection
The type of material used for both the molds and the final product plays a pivotal role in determining the quality and performance of the produced parts. Selecting the right materials ensures that the molds can withstand the pressures and temperatures during production.
2. Mold Design
A well-thought-out mold design can significantly impact the efficiency of the molding process. Factors such as cooling channels, ejection features, and parting lines must be carefully considered to enhance productivity.
3. Machinery and Equipment
The choice of machinery and equipment used in tooling molding also affects the overall quality of the production process. Advanced machinery can lead to better accuracy and reduction in cycle times.
Challenges in Tooling Molding
Despite its advantages, tooling molding presents several challenges that metal fabricators must navigate:
1. High Initial Costs
Creating molds can be expensive, and the initial investment might deter smaller companies from adopting this method. However, the long-term cost savings can outweigh these early costs.
2. Design Complexity
As products become more complex, the design of the molds also increases in intricacy. This complexity requires highly skilled engineers and precise equipment, which can add to production timelines.
3. Maintenance Requirements
Molds require regular maintenance to ensure continued precision and functionality. Neglecting mold care can lead to defects in produced parts.
DeepMould.net: A Leader in Tooling Molding Solutions
At DeepMould.net, we take pride in our exceptional tooling molding services specifically tailored for the metal fabrication industry. Our comprehensive approach combines cutting-edge technology with expert craftsmanship to deliver the highest quality molds that meet the diverse needs of our clients.
Innovative Techniques
We utilize state-of-the-art equipment and advanced techniques to create molds that not only meet but exceed industry standards. Our commitment to innovation allows us to provide tailored solutions for any fabrication challenge.
Skilled Workforce
Our team of highly skilled professionals is our greatest asset. Each member of our workforce is dedicated to ensuring the success of our projects, leveraging their extensive knowledge and experience in tooling molding.
Client-Centric Approach
At DeepMould.net, we prioritize our clients' needs. From the initial consultation to project completion, we ensure open communication and collaboration, tailoring our services to meet individual requirements.
Conclusion
Tooling molding stands as a vital component of the metal fabrication industry, enabling high precision, cost-effectiveness, and speed in the production of metal parts. By leveraging advanced techniques and technologies, businesses like DeepMould.net are leading the charge in developing innovative solutions that cater to the evolving demands of the industry.
As we continue to push the boundaries of what’s possible in tooling molding, we invite you to explore how our services can help optimize your production processes and enhance the quality of your products. Together, we can shape the future of metal fabrication.